Project: The “Brick Sleeve” for AGV units
Partners: SEW-EURODRIVE and SICK Canada
Principal Investigator: Hassan L. Hassan
Students: Anxhelo Mecollari, Christopher Tonon, John Kyle Frias, Lucas Rossi, Divoi K. Morrison
The Automated Guided Vehicle (AGV) has been a staple tool for carrying heavy cargo across various industrial facilities. However, handling large-sized payloads with certain AGV models is a challenge which often results in a company having to purchase a more robust AGV for this purpose.
SEW-EURODRIVE, a pioneer in drive-based automation, and a partner of the Barrett Centre for Technology Innovation (Barrett CTI) approached the team with the idea to create an extension, or sleeve, on top of an existing AGV to extend the surface area of the AGV and balance a large-sized payload.
Through a collaboration with faculty member Hassan Hassan and Mechanical Engineering students Anxhelo Mecollari, Christopher Tonon, John Kyle Frias, Lucas Rossi and Divoi K. Morrison, the research team focused on making a special application for existing Brick-type AGVs to handle loads up to 500kg.The team quickly devised a roadmap, including a drawing and 3D build of the sleeve. Despite the challenge of working remotely because of the COVID-19 pandemic, Hassan and the student team continued to edit and improve their design for an eventual assessment by SEW-EURODRIVE.
The team first tried to use the AGV itself by placing a frame on top of it. “While we were doing our calculation and research, we realized that wasn’t going to work. We also found out that the Brick [AGV] itself has more capacity of pulling. We kind of positioned the whole frame around it so it works like a truck…like a trailer type of idea,” Mecollari said.
“We added a second sensor that will give us a 360 [degree] view, so even if something comes close, on the side of the AGV, it will be able to keep a safe distance or even stop if it’s not possible to move away,” he said.
SEW-EURODRIVE provided several Brick AGVs to the team as a template to work with. Sensors generously provided by another Barrett CTI partner, SICK Canada, also allowed the enhanced AGV to safely move past obstacles in busy warehouses. Humber’s Office of Applied Research & Innovation funded the project’s sleeve components.
For Hassan, his favourite part of the project was watching students push themselves to address SEW-EURODRIVE’s requirements.
“A lot of students don’t realize that design isn’t one simple process,” Hassan said. “It’s a lot of back and forth. A lot of revisions until they come up with a final version, and if I can call it the final, there’s nothing really final. Everything evolves, changes and there’s always room for development.”
“I think it’s going to open a big door for them to create more of these extensions to do more in specialized and specific jobs,” Hassan said.
The team’s next step is in improving their Brick Sleeve design until it is ready for a hard evaluation with SEW-EURODRIVE after the COVID-19 pandemic. As industries are expected to move full-speed ahead, Hassan and the research assistants hope their Brick Sleeve solution can help SEW-EURODRIVE’s customers be more productive and profitable.
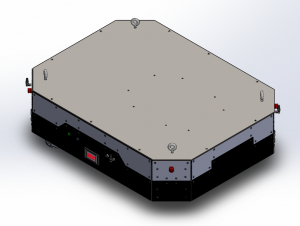